ニュース
メディア
現代の製造業における粉末冶金の利点
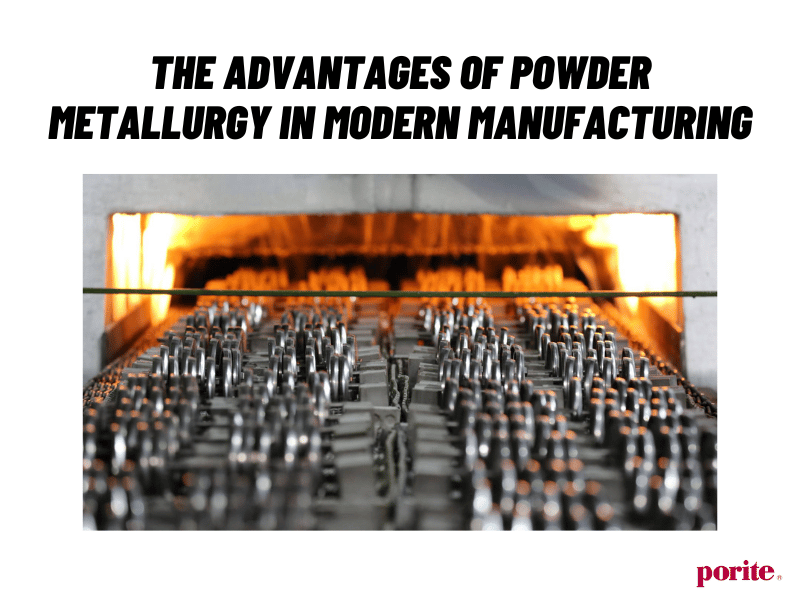
概要粉末冶金
粉末冶金(PM)は、金属粉末を圧縮および焼結して精密な部品を製造する、非常に効率的な製造プロセスです。この技術は、自動車、航空宇宙、産業機械、電子機器などの多くの産業分野で広く利用されており、鋳造、鍛造、機械加工といった従来の金属加工方法に比べて多くの利点があります。
本記事では、粉末冶金の主要な利点である材料効率、コスト効果、設計の柔軟性について解説し、従来の製造技術と比較します。
________________________________________
粉末冶金の主な利点
利点1. 優れた材料効率
粉末冶金の最大の利点の一つは、原材料の使用効率を最大化できることです。従来の機械加工では余分な材料を削り取りますが、PMプロセスでは原材料のほぼ100%を使用します。これにより廃棄物が減少し、材料コストが削減され、環境に優しい持続可能な製造手法となります。
従来工法との比較
- 鋳造・鍛造:ランナー、ゲート、バリなどの余分な材料が発生し、追加の加工や再処理が必要。
- 機械加工:大量のスクラップ金属が発生し、材料コストが増加。
- 粉末冶金:必要な分の金属粉末のみを使用し、廃棄物を最小化。
利点2. コスト効率と生産コストの削減
粉末冶金は、大量生産に特に適した、コスト効率の高い製造方法です。コスト削減に寄与する要素は以下の通りです:
- 材料コストの削減:ニアネットシェイプ成形により、大幅な機械加工が不要。
- エネルギーの節約:鋳造や鍛造に比べて、低温での処理が可能。
- 二次加工の最小化:PMで作られた部品は、追加の機械加工や熱処理がほとんど不要。
- 高い生産性:大量の自動生産に適しており、人件費を削減。
従来工法との比較
- 鋳造:高エネルギー消費と広範な仕上げ加工が必要。
- 鍛造:高価な金型と高圧装置が必要。
- 機械加工:時間がかかり、スクラップの発生でコストが増大。
利点3. 柔軟な設計と複雑な形状の実現
粉末冶金では、従来の製造方法では困難または不可能な複雑な形状や精密な設計が可能です。機械加工を多用せずに詳細なデザインを実現できるため、特定の材料特性を持つ精密部品の製造に最適です。
設計上の利点
- 複数の機能を一体化した部品の製造が可能。
- 内部空洞を含む独自形状の製造が可能。
- 高い寸法精度と再現性。
- 自己潤滑ベアリングやフィルターのような特殊用途向けに、制御された多孔性の部品製造が可能。
従来工法との比較
- 鋳造・鍛造:形状に制限があり、望ましい形状にするには複数の工程が必要。
- 機械加工:複雑な形状の製造は可能だが、時間とコストがかかる。
利点4. 優れた材料特性と性能
粉末冶金では、材料組成を正確に制御することができ、機械的・物理的特性を向上させることが可能です。これは、耐摩耗性、耐腐食性、特定の硬度が求められる用途に非常に有効です。
- 高強度・高耐久性の部品設計が可能。
- 制御された多孔性により、含油ベアリングなどの用途に対応。
- 熱処理や合金化によって、用途に合わせた特性のカスタマイズが可能。
従来工法との比較
- 鋳造:収縮や多孔性といった内部欠陥が発生しやすい。
- 鍛造:強度は高いが、精密加工が必要。
- 機械加工:材料特性は高いが、廃棄が多い。
利点5. 持続可能性と環境への配慮
持続可能な製造が重視される現代において、粉末冶金は環境に配慮したプロセスとして注目されています。
- 廃棄物の削減:材料のほぼ100%を活用。
- エネルギー消費の低減:鋳造・鍛造に比べてエネルギー使用量が少ない。
- リサイクルへの対応:金属粉末はリサイクル素材から調達可能で、環境負荷を軽減。
従来工法との比較
- 鋳造:高いエネルギー消費と排出量。
- 鍛造・機械加工:大量の廃棄物を発生。
________________________________________
結論
粉末冶金は、従来の製造方法に比べて数多くの利点を持つ、変革的な製造技術です。高い材料効率、コストパフォーマンス、設計の柔軟性、優れた機械的特性、環境持続性により、PMは高品質な精密部品製造における最適な選択肢となりつつあります。
産業界がより高度な製造ソリューションを求める中で、粉末冶金は今後も革新の中核として進化を続け、現代製造における比類なき効率と性能を提供していきます。
自動車部品、航空宇宙部品、産業用アプリケーションなど、PMは金属加工の未来を切り開いています。
ご興味のある粉末冶金の具体的な応用分野について、さらに詳しくご紹介しましょうか? ぜひ、お知らせください!Let us know!